Selecting the right woodworking machinery supplier in China is crucial for ensuring quality, efficiency, and value in your operations. China’s market offers a vast array of suppliers, making it essential to understand key factors that can help you make an informed decision.
1. Understand Your Requirements
Before approaching suppliers, clearly define your specific needs. Consider the following:
- Type of Machinery: Are you looking for CNC routers, saws, planers, or sanders?
- Volume and Scale: What is your production scale? Do you need industrial-grade machines for high-volume production or smaller, more versatile equipment for custom work?
- Technical Specifications: What are the essential specifications such as power, speed, and capacity?
2. Research and Identify Potential Suppliers
Begin your search by identifying reputable suppliers. Here’s how:
- Industry Exhibitions and Trade Shows: Attend events like the China International Woodworking Machinery Fair to meet suppliers and see their products firsthand.
- Online Marketplaces: Platforms like Alibaba and Made-in-China offer extensive listings of woodworking machinery suppliers.
- Industry Associations: Engage with associations like the China National Forest Machinery Association for recommendations.
3. Evaluate Supplier Credentials
Not all suppliers are created equal. Assess their credentials by considering:
- Certifications: Look for suppliers with relevant certifications such as ISO 9001 for quality management.
- Experience: Prefer suppliers with extensive experience in the woodworking machinery industry.
- References and Reviews: Check reviews and ask for references to gauge reliability and customer satisfaction.
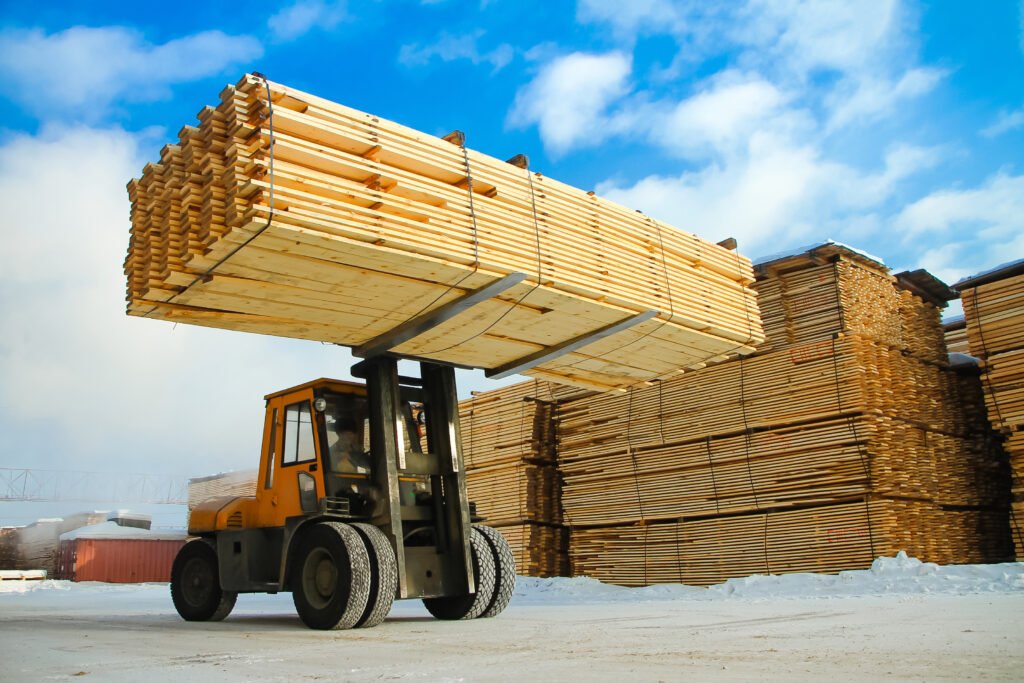
4. Assess Product Quality and Innovation
Quality and technological advancement are critical for efficiency and long-term reliability. Evaluate:
- Product Range: Ensure the supplier offers a range of products that meet your current and future needs.
- Technology: Look for suppliers investing in modern technology and innovation to provide state-of-the-art machinery.
- Testing and Quality Assurance: Inquire about their quality control processes and product testing protocols.
5. Review Pricing and Payment Terms
While price should not be the sole determining factor, it is essential to understand:
- Competitive Pricing: Compare quotes from multiple suppliers to get a fair price.
- Payment Terms: Understand the payment structure, including deposits, milestones, and final payments.
- Total Cost of Ownership: Consider not just the purchase price but also maintenance, spare parts, and operational costs.
6. Examine After-Sales Support
Strong after-sales support ensures minimal downtime and ongoing productivity. Look for:
- Warranty: Evaluate the warranty terms and what they cover.
- Technical Support: Ensure the supplier offers reliable technical support, including remote assistance and on-site service.
- Spare Parts Availability: Check the availability and lead time for spare parts.
7. Verify Logistics and Delivery
Efficient logistics and timely delivery are essential for seamless operations. Consider:
- Shipping Terms: Understand the shipping terms and responsibilities.
- Lead Time: Verify the lead time for manufacturing and delivery.
- Customs and Import Regulations: Ensure compliance with local customs and import regulations.
8. Visit the Supplier’s Facility
If feasible, visit the supplier’s manufacturing facility to:
- Inspect Production Lines: Assess the production lines and quality control processes.
- Meet the Team: Meet the management and technical teams to gauge their expertise and professionalism.
- Evaluate Infrastructure: Check the infrastructure to ensure it supports high-quality manufacturing.
9. Negotiate and Secure a Contract
Once you have shortlisted suppliers:
- Negotiate Terms: Discuss and negotiate terms of purchase, delivery, and after-sales support.
- Draft a Detailed Contract: Ensure the contract clearly outlines product specifications, pricing, delivery timelines, warranty terms, and support details.
10. Continuous Review and Feedback
Post-purchase, continuously review the supplier’s performance and provide feedback. This helps maintain a strong relationship and ensures any issues are promptly addressed.
Conclusion
Choosing the right woodworking machinery supplier in China involves careful consideration of your specific needs, supplier credentials, product quality, pricing, after-sales support, and logistics. By following these guidelines, you can select a supplier that offers high-quality machinery and reliable support, ensuring efficiency and productivity in your woodworking operations.
By following these steps, you will be well-equipped to find a woodworking machinery supplier in China that aligns with your business needs and provides excellent value.